Stopy magnezu o podwyższonej wytrzymałości przetwarzane technologią Selektywnego Topienia Laserowego do zastosowań lotniczych i kosmicznych
Magnesium based alloys for components of increased strength manufactured with Selective Laser Melting for aerospace applications
cele projektu
Projekt dotyczy opracowania materiału oraz technologii wytwarzania ultralekkich elementów dla potrzeb przemysłu lotniczego i kosmicznego o skomplikowanej geometrii
oraz podwyższonej wytrzymałości ze stopów magnezu w tym m.in. zbiorników i aparatury paliwowej rakiet suborbitalnych. Elementy będą wytwarzane metodą Selektywnego Topienia Laserowego – SLM.
Opracowana technologia pozwoli na wytwarzania elementów
o podwyższonej wytrzymałości mechanicznej oraz wysokiej wytrzymałości zmęczeniowej. Badania realizowane w ramach projektu prowadzone będą w oparciu o stop magnezu AZ91E, niestosowany obecnie w przyrostowych metodach wytwarzania. Podczas realizowanych prac zostaną opracowane mieszaniny na bazie proszku AZ91E z dodatkami stopowymi w postaci proszków Ti6Al4V oraz Sc. Następnie dla tych, nowych materiałów zostaną opracowane parametry procesu SLM celem wykonania elementów testowych. Materiał przetworzony laserowo, będzie poddawany bieżącej szczegółowej analizie uwzględniającej: pomiar gęstości i analizę mikrostruktury
(w celu określenia porowatości materiału po spiekaniu) analizę składu chemicznego (EDS) i fazowego (XRD), analizę właściwości mechanicznych (wytrzymałość na rozciąganie), pomiar i analizę dokładności wykonania i jakości warstwy wierzchniej, odporność na korozję. W ramach prowadzonych prac zostaną również opracowane parametry dogęszczania materiałów metodą HIP (Hot Isostatic Pressing) oraz technologia obróbki cieplnej wytworzonych elementów. W ramach projektu, wykorzystując opracowane materiały i technologię, zostanie wykonany oraz zweryfikowany w warunkach laboratoryjnych zbiornik paliwa rakiety suborbitalnej.
W efekcie realizacji projektu zostaną opracowane nowe stopy / kompozyty na bazie magnezu oraz powstanie nowa wiedza dotycząca wpływu parametrów rozwijanych procesów SLM na wybrane właściwości elementów.
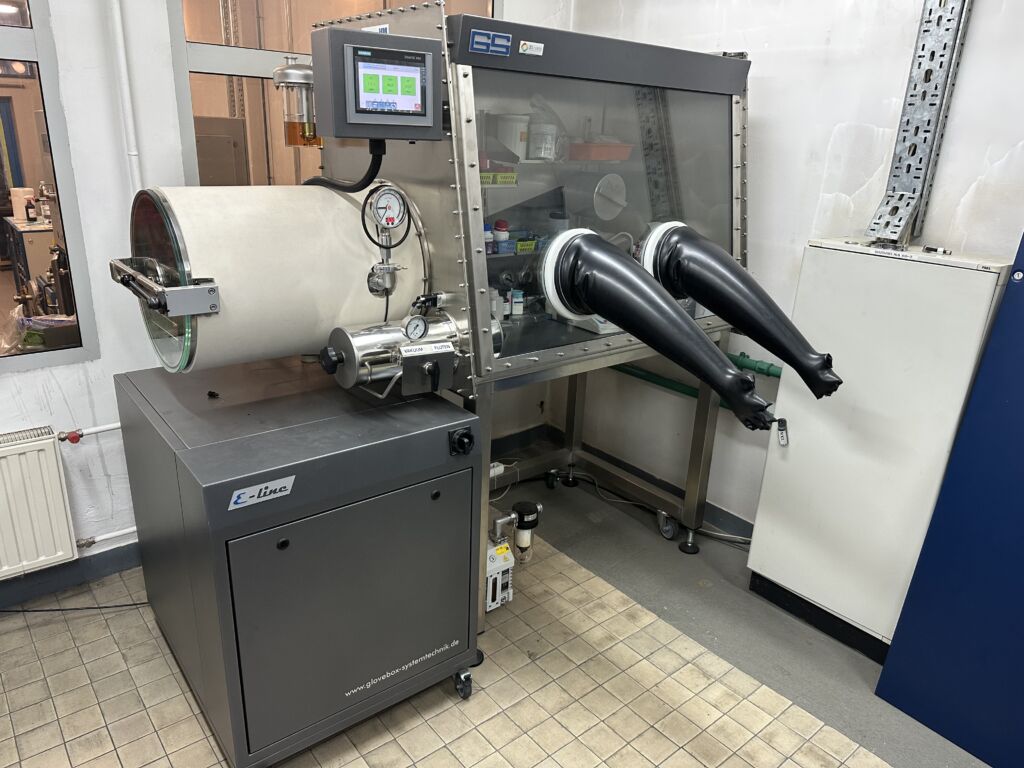
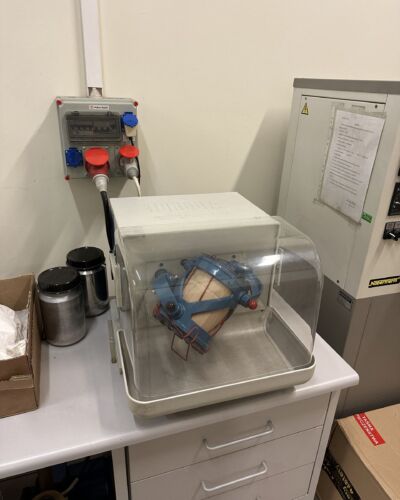
Ł - KIT - Lider
Dr inż. Andrzej Stwora
10.2004 r.-03.2020 r. zatrudniony w Instytucie Zaawansowanych Technologii Wytwarzania. Od 04.2020 r. – obecnie Łukasiewicz -Krakowski Instytut Technologiczny w Krakowie, w Centrum Materiałów i Technologii Wytwarzania. Od początku pracy
w Instytucie odpowiedzialny za realizację doświadczeń oraz rozwój wykorzystywanej aparatury badawczej z zakresu obróbki elektrochemicznej oraz przyrostowych metod wytwarzania
i inżynierii odwrotnej. Od roku 2011 do chwili obecnej prowadzi prace związane z technologią Selektywnego Spiekania
i Topienia Laserowego SLS/SLM. W ramach prowadzonych prac m.in. została przeprowadzona optymalizacja parametrów spiekania proszków stopu tytanu Ti6Al4V, Tytan – Tantal, Tytan – Molibden, czysty Tytan pod kątem dogęszczenia wyrobu.
Przeprowadzono doświadczenia związane
z budową elementów, w tym lekkich struktur
z wykorzystaniem proszków nadstopu niklu Inconel 718, oraz stopu aluminium AlSi10. Wykonane elementy zostały poddane próbom wytrzymałościowym oraz sprawdzono strukturę geometryczną uzyskanych modeli.
Jest współautorem prawie 40 artykułów naukowych dotyczących metod przyrostowych SLS/SLM oraz metod erozyjnych, legitymuje się Indeksem Hirsha w bazie Scopus 6.
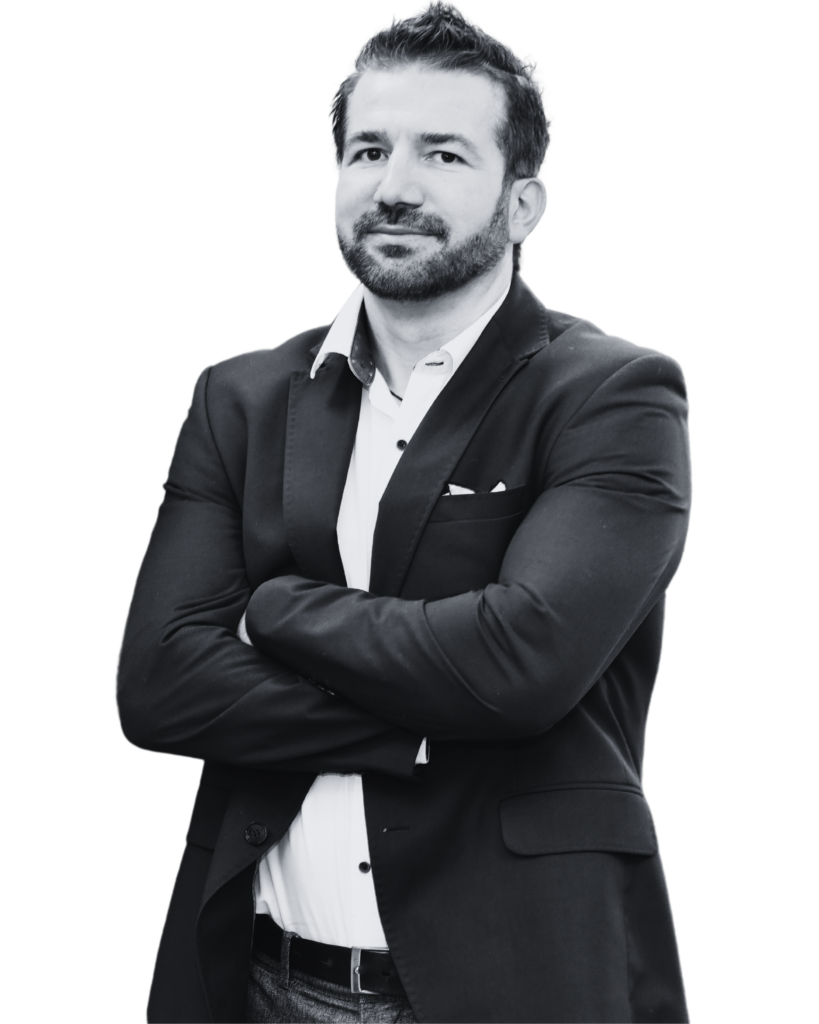
Dr inż. Jolanta Laszkiewicz-Łukasik
Specjalista z dziesięcioletnim stażem pracy, operator skaningowego mikroskopu elektronowego Jeol 6460LV wraz
ze spektrometrami EDS i WDS oraz systemem EBSD (Oxford Instruments). Jako pracownik laboratorium akredytowanego posiada uprawnienia do autoryzacji i wykonywania
usług w zakresie analizy morfologii i mikrostruktury materiałów przy pomocy SEM. Realizacja usług dla przemysłu, w tym np. firm Synthos, Valeo Autosystemy, Fertinger Automotive, czy też Ministerstwa Kultury i Dziedzictwa Narodowego.
Wieloletnie doświadczenie w technologiach spiekania materiałów, w tym spiekania swobodnego, mikrofalowego oraz wysokociśnieniowego (High Pressure High Temperature), a także metodą Spark Plasma Sintering.
Ściśle współpracuje z przemysłem w zakresie rozwiązywania problemów materiałowych, technologicznych i obróbkowych. Prace rozwojowe w zakresie opracowania innowacyjnych narzędzi skrawających
z wymiennymi płytkami węglikowymi do rowkowania i przecinania metalu i jego stopów.
Wartość prowadzonych badań znalazła potwierdzenie w 35 publikacjach naukowych,
w tym 13 indeksowanych w bazie Scopus. Legitymuje się Indeksem Hirsha 6.
Scopus, m.in. w czasopismach Metals, Processing and Application of Ceramics, International Journal of Refractory Metals and Hard Materials, International Journal of Advanced Manufacturing Technology, Diamond and Related Materials.
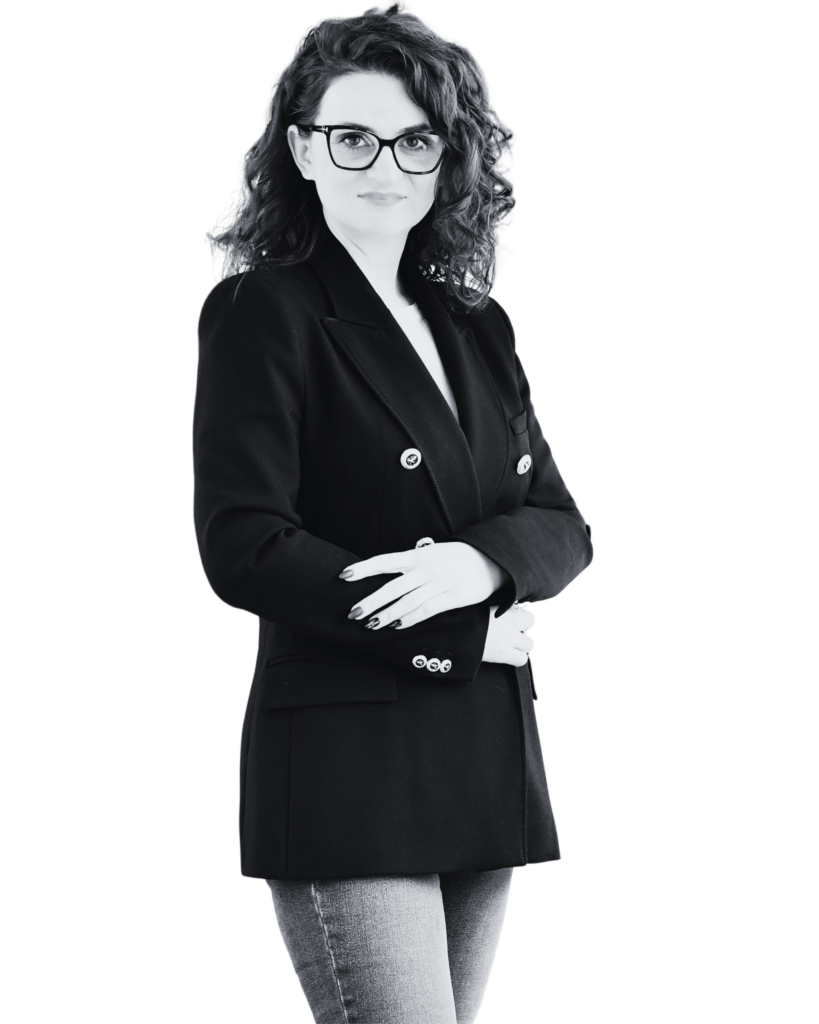
Dr inż. Rafał Dziurka
W 2008 roku rozpoczął Studia Doktoranckie na Wydziale Metalurgii i Inżynierii Materiałowej AGH
w Krakowie w Dyscyplinie Inżynieria Materiałowa. Posiada duże doświadczenie związane z wytwarzaniem materiałów niskostopowych domieszkowanych pierwiastkami pośrednimi m.in. bor, a także z analizą wpływu obróbek cieplnych podczas odpuszczania na przemiany fazowe m.in. stali stopowych Mn−Cr−Mo.
Brał udział w 26 konferencjach i warsztatach – 20 referatów, 6 posterów.
Aktywnie uczestniczy w realizacji projektów naukowo badawczych na zlecenie m.in. dla Celsa Huta Ostrowiec; ArcelorMittal Poland; Pratt&Whitney Kanada Corp.; PROPART; „Śrubena Unia” Żywiec; Iskra Centrum Narzędzi Specjalnych sp. z o.o.;
Solaris Bus & Coach S.A.; Aesculap Chifa Sp. z o.o.; WARTA 24 PLUS Sp. z.o.o; Valeo Autosystemy sp. z o.o.; Dürr Poland Sp.z o.o.; UTC CCS Manufacturing Polska Sp. z o.o.; Łańcuchy Galla Sp. z o.o.
Jest autorem 126 publikacji naukowych, w tym 16 w czasopiśmie z Listy Filadelfijskiej i 54 publikacje z PM i 56 referatów, Index H = 8 w tym 212 cytacji.
Zrealizowane i realizowane projekty badawcze.
Udział w 14 grantach NCN, PBS i NCBiR, jako wykonawca.
Dr Ewa Rząd
Od 2019 roku jest pracownikiem w Sieć Badawcza ŁUKASIEWICZ –Krakowski Instytut Technologiczny. W swojej pracy zawodowej zajmuje się prowadzeniem testów korozyjnych w wysokich temperaturach (550–1100°C), korozją elektrochemiczną, biokorozją, modyfikacją powierzchniową materiałów (powłoki dyfuzyjne, powłoki warstwa po warstwie), syntezą nanomateriałów oraz analiza powierzchni skaningowym mikroskopem elektronowym (SEM). Posiada duże doświadczenie z badania korozyjności m.in stopów AZ91 w podwyższonej temperaturze, wykonanych metodą odlewania.
Jest współautorem 13 publikacji, legitymuje się Indeksem Hirsha
w bazie Scopus 6.
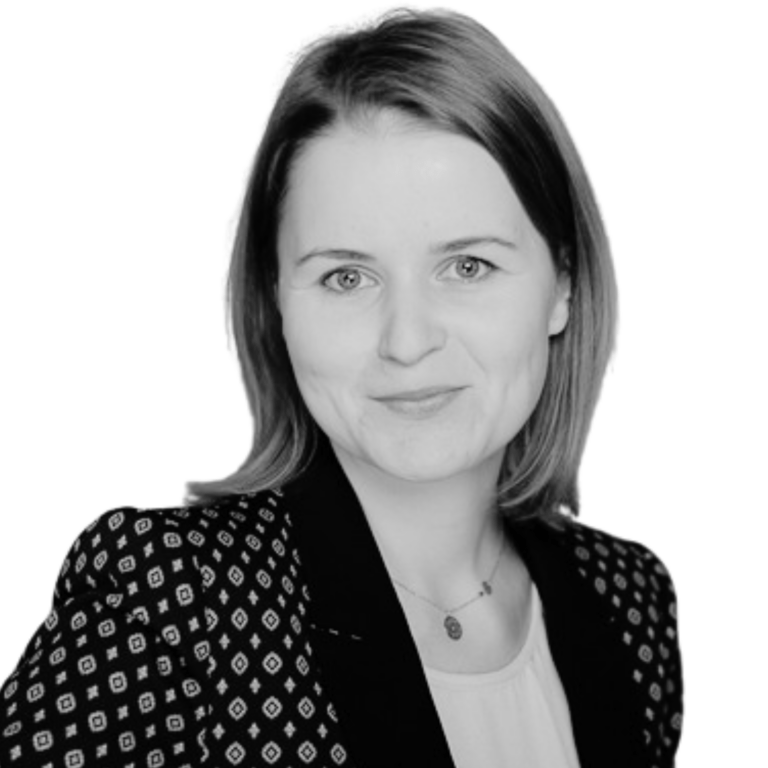
Dr inż. Marcin Podsiadło
Jest absolwentem kierunku inżynieria materiałowa (2010-2015) na Wydziale Inżynierii Metali i Informatyki Przemysłowej Akademii Górniczo-Hutniczej (studia inżynierskie) oraz edukacja techniczno – informatyczna na Wydziale Matematyczno – Fizyczno – Technicznym Uniwersytetu Pedagogicznego (studia magisterskie).
Obecnie jest studentem studiów doktoranckich w ramach programu „Doktorat wdrożeniowy” na Wydziale Metali Nieżelaznych Akademii Górniczo-Hutniczej. Tematem mojej pracy jest „Lutowanie wkładek ceramicznych, szczególnie
o osnowie diamentowej z korpusem narzędzia przeznaczonego do obróbki skrawaniem”.
Od czerwca 2006 r. zatrudniony w Instytucie Zaawansowanych Technologii Wytwarzania (obecnie Sieć Badawcza Łukasiewicz – Krakowski Instytut Technologiczny) w Krakowie, Centrum Inżynierii Materiałowej i Technik Spiekania. Jako pracownik laboratorium akredytowanego posiada uprawnienia do autoryzacji i wykonywania usług w zakresie prowadzenia i kontroli badań jakościowych podczas trwania projektów na bieżąco tj. wykonanie zgładów , badania gęstości metodą Archimedesa, twardości, moduł Younga.
Aktywnie uczestniczy w realizacji projektów badawczych i rozwojowych finansowanych ze źródeł własnych Instytutu
oraz m.in.: liczne prace związane z zagadnieniami inżynierii materiałowej m.in. wytwarzanie materiałów supertwardych, (diamentów) metodą HPHT – Synteza (spiekanie) diamentowych polikryształów, spiekania swobodnego przy współpracy
z przedsiębiorstwami (m.in. Reszka, Polkom, Createk, Gopol itp.). Jest współautorem prawie 20 artykułów naukowych dotyczących prowadzonych badań związanych z zagadnieniami inżynierii materiałowej w renomowanych czasopismach potwierdzenie , m.in. w czasopismach Metals, Processing and Application of Ceramics, International Journal of Refractory Metals and Hard Materials, International Journal of Advanced Manufacturing Technology, Diamond and Related Materials. legitymuje się Indeksem Hirsha w bazie w bazie Scopus 6.
realizacja projektu
harmonogram

Obecnie projekt jest w fazie realizacji (Zadanie 1), które realizuje Ł – KIT (Wnioskodawca) pt. Przygotowanie stanowiska badawczego przystosowanego do pracy z materiałami silnie reaktywnymi oraz opracowanie składu i wytwarzanie modyfikowanych…
- Wykonanie stanowiska zapewniającego czystość atmosferyczną poniżej 100 ppm tlenu w komorze roboczej przy temperaturze pokojowej.
Badania i optymalizacja procesu ważenia i mieszania wsadu
w warunkach laboratoryjnych.
Wszystkie badania w ramach zadania 1, będą prowadzone
w warunkach laboratoryjnych z zastosowaniem urządzenia prototypowego, którego konstrukcja, cechy funkcjonalne
i parametry będą modyfikowane w zależności od wyników
i postępów badań.
CEL (Zadanie 1):
Uzyskanie co najmniej 3 mieszanin proszkowych o założonym rozkładzie cząstek tj. mieszanina proszkowa stopu AZ91E oraz Skandu (Sc), mieszanina proszkowa stopu AZ91E z stopem Ti6Al4V oraz mieszanina stopu AZ91E z Sc oraz Ti6Al4V.
Przynajmniej 90% wag. cząstek w badanej partii proszku (parametr D90) powinno mieć rozmiar poniżej 48 μm.
System obsługi proszku na bazie Mg.
Opracowany kompletny system wytwarzania mieszanin proszkowych pozwalający na ograniczenie ilości tlenu do 100 ppm (pomiar w wybranych punktach) w komorze roboczej.
Aktualności:
W dniach 24–26 czerwca 2025 r. dr inż. Andrzej Stwora oraz dr inż. Jolanta Laszkiewicz-Łukasik z Centrum Materiałów i Technologii Wytwarzania Łukasiewicz – Krakowskiego Instytutu Technologicznego uczestniczyli w wizycie studyjnej w Joint Research Centre (JRC) Komisji Europejskiej w Ispra we Włoszech.
W wydarzeniu wzięło udział jedynie dziesięciu młodych naukowców z Polski – laureatów XIII i XIV edycji programu LIDER Narodowego Centrum Badań i Rozwoju. Z dumą informujemy, że dwóch z nich reprezentowało nasz Instytut.
Joint Research Centre to wewnętrzna jednostka badawcza Komisji Europejskiej, która odgrywa istotną rolę w procesie tworzenia polityk Unii Europejskiej opartych na dowodach naukowych i rzetelnej analizie. Centrum prowadzi m.in.:
analizy eksperckie,
modelowanie danych,
prace badawcze dotyczące obronności, zdrowia publicznego, bezpieczeństwa oraz zrównoważonego rozwoju.
Podczas wizyty przedstawiciele Instytutu:
uczestniczyli w sesjach laboratoryjnych,
prezentowali własne projekty badawcze,
odbyli spotkania z badaczami JRC,
omawiali potencjalne kierunki współpracy z instytucjami Unii Europejskiej.
Wizyta była elementem działań towarzyszących prezydencji Polski w Radzie Unii Europejskiej i stanowiła istotny krok w kierunku wzmacniania roli nauki i innowacji w budowaniu nowoczesnej Europy. Wyjazd został zorganizowany na zaproszenie Narodowego Centrum Badań i Rozwoju oraz Ministerstwa Nauki i Szkolnictwa Wyższego.
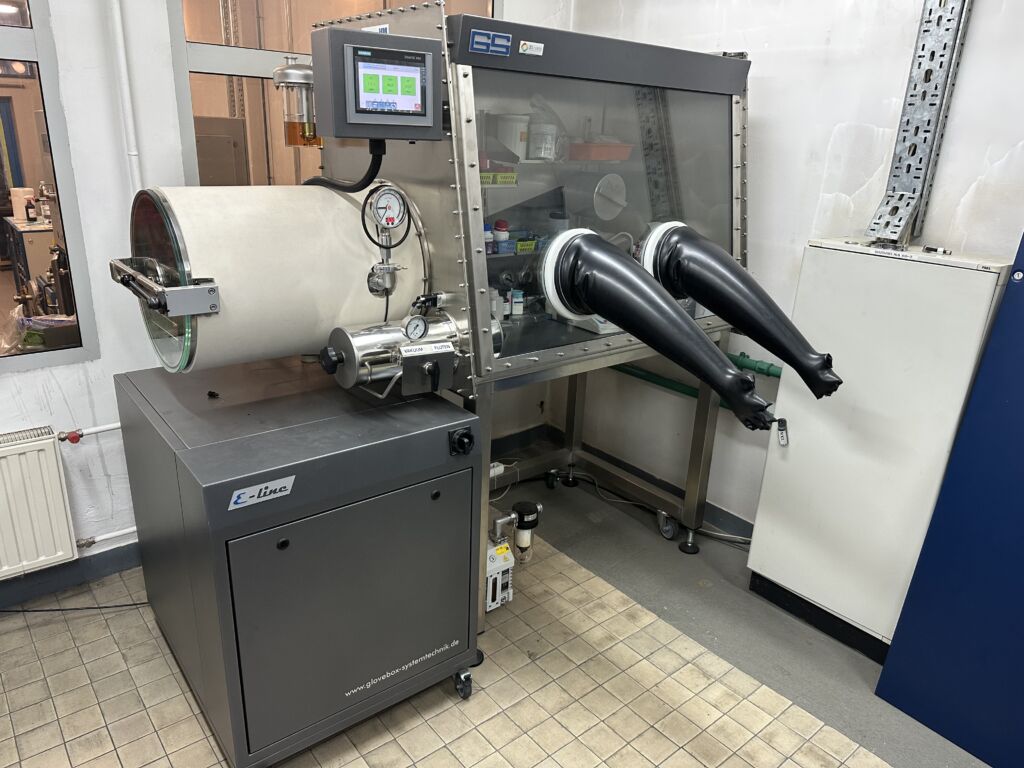
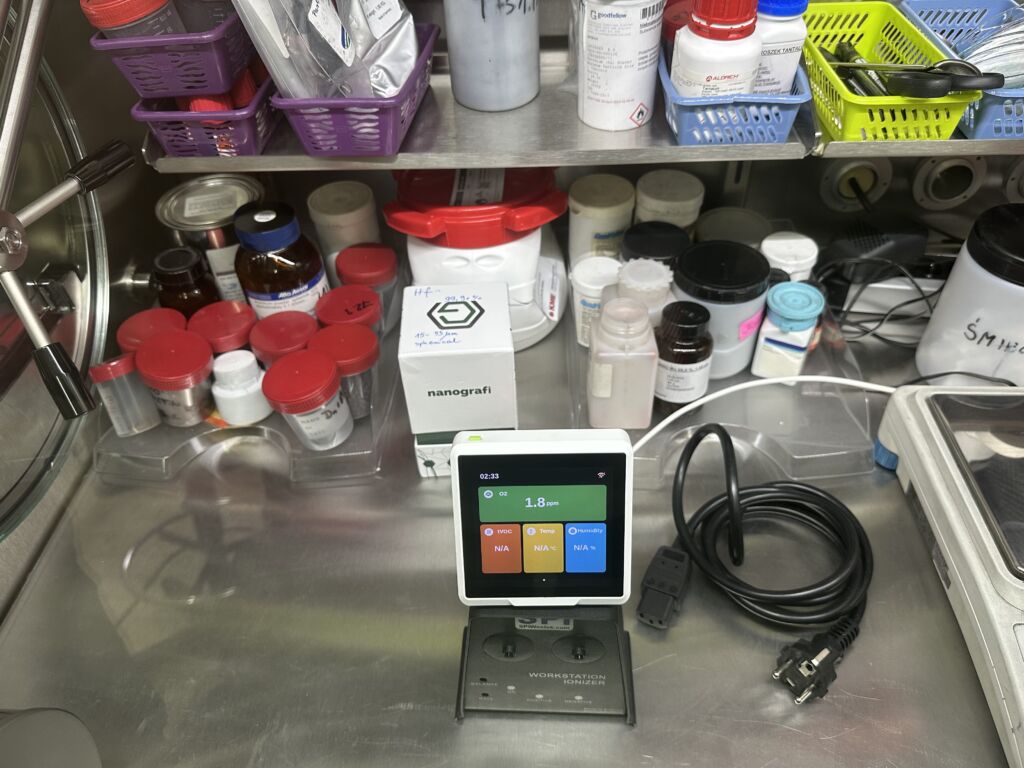
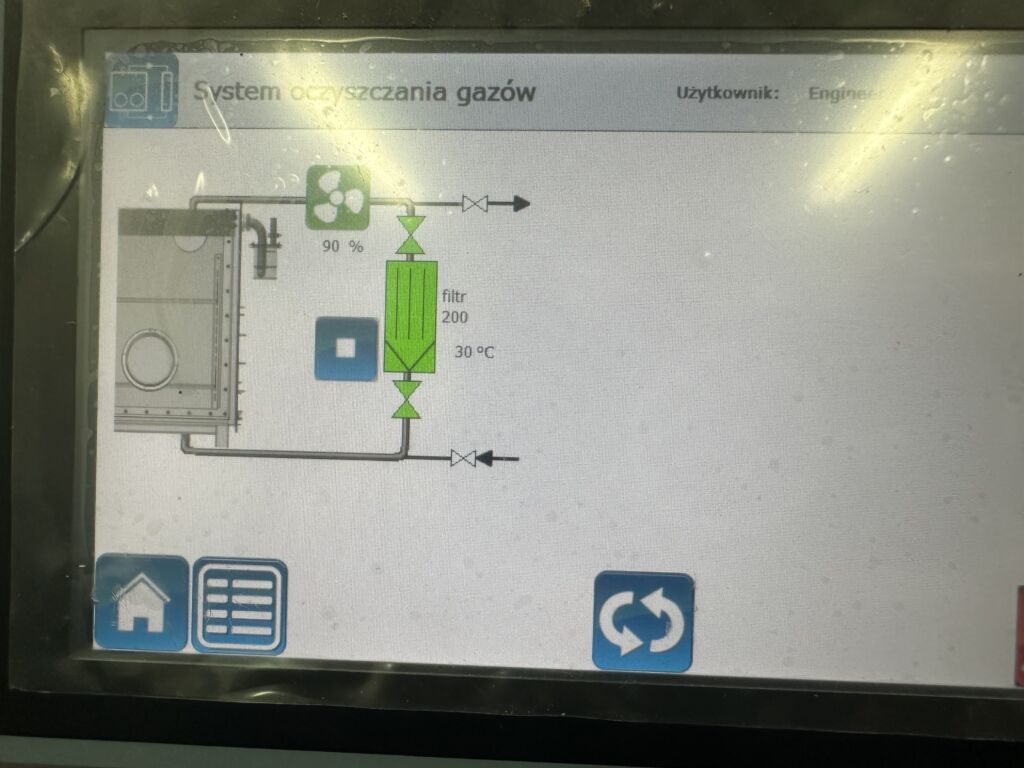
finansowanie
Narodowe Centrum Badań i Rozwoju NCBR
Numer wniosku o dofinansowanie: 0238/L-14/2023
Numer konkursu: LIDER XIV
Wartość Projektu
1 799 657,50 PLN
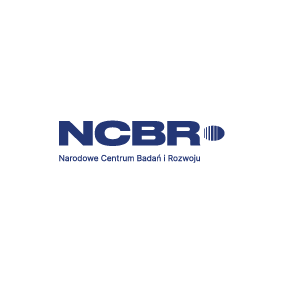