Centrum Materiałów i Technologii Wytwarzania
Centrum Materiałów i Technologii Wytwarzania (CMW) to zespół naukowców, o wyspecjalizowanej ekspertyzie w dziedzinie inżynierii materiałowej, zajmujących się projektowaniem i rozwojem nowoczesnych technik wytwarzania oraz technologii związanych z kształtowaniem, obróbką i badaniami materiałów.
Głównym celem pracy CMW jest prowadzenie zaawansowanych badań naukowych oraz opracowywanie innowacyjnych technologii wytwarzania, obejmujących wszystkie etapy procesu od koncepcji do finalnego produktu. Realizowana tematyka badawcza wspiera rozwój różnych sektorów gospodarki poprzez wprowadzenie nowatorskich rozwiązań w inżynierii materiałowej, przy jednoczesnym uwzględnieniu konkretnych zastosowań dla przemysłu odlewniczego, lotniczego i energetycznego. W ramach swojej działalności CMW koncentruje się na rozwijaniu w następujących obszarach badawczych:
Obszary działalności CMW:
- Obszar Technik Spiekania oraz Materiałów i Procesów Proszkowych
- Obszar Obróbki Skrawaniem i Narzędzi
- Obszar Wytwarzania Addytywnego oraz Selektywnego Spiekania i Topienia Laserowego
- Obszar Badań Wysokotemperaturowych
- Obszar Badań Korozji Wysokotemperaturowej
- Obszar Stopów Odlewniczych
- Obszar Projektowania i Prototypowania
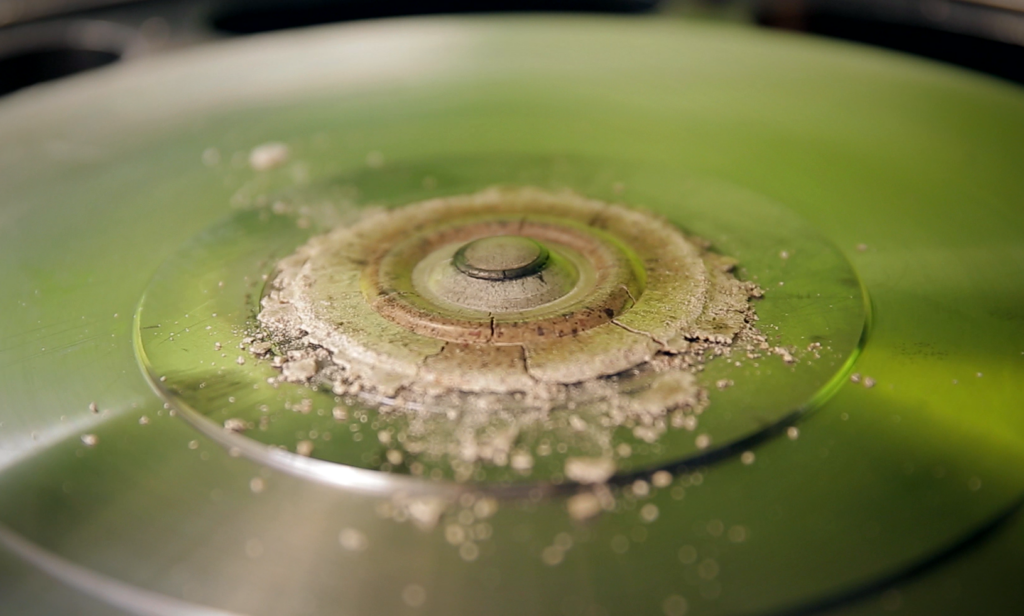
Obszar Technik Spiekania oraz Obszar Materiałów i Procesów Proszkowych
W obszarach prowadzone są badania mające na celu Rozwój technologii kompozytów ceramicznych, w tym supertwardych oraz kompozytów z udziałem materiałów z recyklingu, otrzymywanych zaawansowanymi metodami spiekania (SPS, HPHT, MW, etc.):
- Materiały supertwarde na bazie regularnego azotku boru do zastosowań w obróbce skrawaniem nadstopów niklu typu Inconel i innych trudnoobrabialnych materiałów, jak również do innowacyjnych zastosowań na elementy elektroniczne, w tym odprowadzające ciepło w elementach elektronicznych dużej mocy.
- Kompozyty ceramiczne, różne rodzaje, otrzymywane głównie metodami SPS – Spark Plasma Sintering oraz HPHT – High Pressure, High Temperature.
Obszar Obróbki Skrawaniem i Narzędzi
W obszarze prowadzone są badania skupiające się na technologiach wytwarzania wyrobów o wysokim stopniu przetworzenia, zwłaszcza metodami obróbki wiórowej i powierzchniowej zgniotem przyczyniające się do ekologicznego i zrównoważonego rozwoju gospodarki opartej na wiedzy, innowacyjności i produktywności.
Trwają pracę nad rozwojem wybranych technologii modyfikacji warstwy powierzchniowej w celu zwiększenia trwałości narzędzi, części maszyn i innych wyrobów – poprzez wykorzystanie różnych metod obróbki, m.in. mechanicznej (toczenie, frezowanie), plastycznej (nagniatanie) czy też tribologicznie zaawansowanych supertwardych powłok PVD o ukierunkowanej jakości użytkowej – zgodnych z koncepcją Przemysłu 4.0.
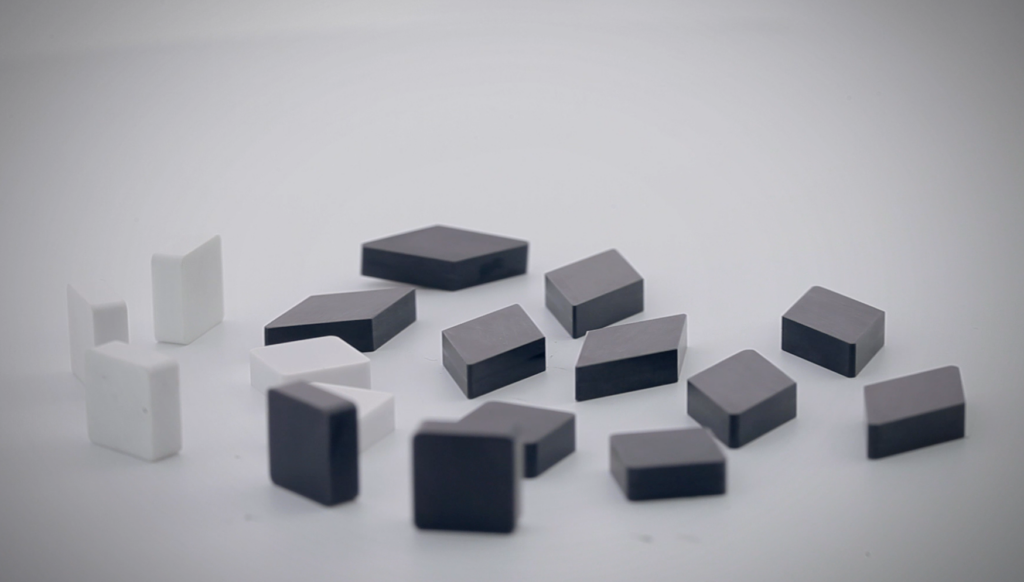
Obszar Wytwarzania Addytywnego oraz Selektywnego Spiekania i Topienia Laserowego
W obszarze prowadzone są badania związane z optymalizacją technologii wytwarzania przyrostowego w oparciu o dostępne w Instytucie urządzenia:
- Binder Jetting (Digital Metal/Markforged DMP2500) – wytwarzanie detali z materiałów metalicznych, ceramicznych (m.in.: ceramika tlenkowa, węgliki spiekane) oraz cermetów dla potrzeb zastosowań biomedycznych (np.: implanty, narzędzia chirurgiczne, elementy manipulatorów), technicznych (np.: dysze dla potrzeb water-jet), militarnych i lotniczych (elementy kamizelek / środków ochrony osobistej oraz osłon termicznych wytwarzanych np. z B4C).
- SLM (Selective Laser Melting), DED/LMD (Direct Energy Deposition/Laser Material Deposition) – stopowanie elementów z mieszanin proszków metalicznych.
- Spiekanie i obróbka termiczna elementów wykonanych metodami przyrostowymi, uwzględniająca m.in.: HIP (hot isostatic pressing).
- Optymalizacja topologiczna elementów z uwzględnieniem dostępnych technologii wytwarzania przyrostowego oraz obróbki ubytkowej.
Dodatkowo prowadzone są badania rozwojowe wybranych technologii obróbki bezstykowej:
- Obróbka elektrochemiczna – kształtowanie złożonych powierzchni elementów z materiałów trudnoskrawalnych (m.in.: nadstopy niklu, węgliki spiekane).
- Wygładzanie elektrochemiczne oraz metodą elektropolerownia plazmowego – poprawa jakości powierzchni detali wytwarzanych metodami przyrostowymi z materiałów przewodzących prąd.
- Modyfikacja warstwy wierzchniej – nakładanie powłok metodą MAO (micro arc oxidation).
Obszar Badań Wysokotemperaturowych
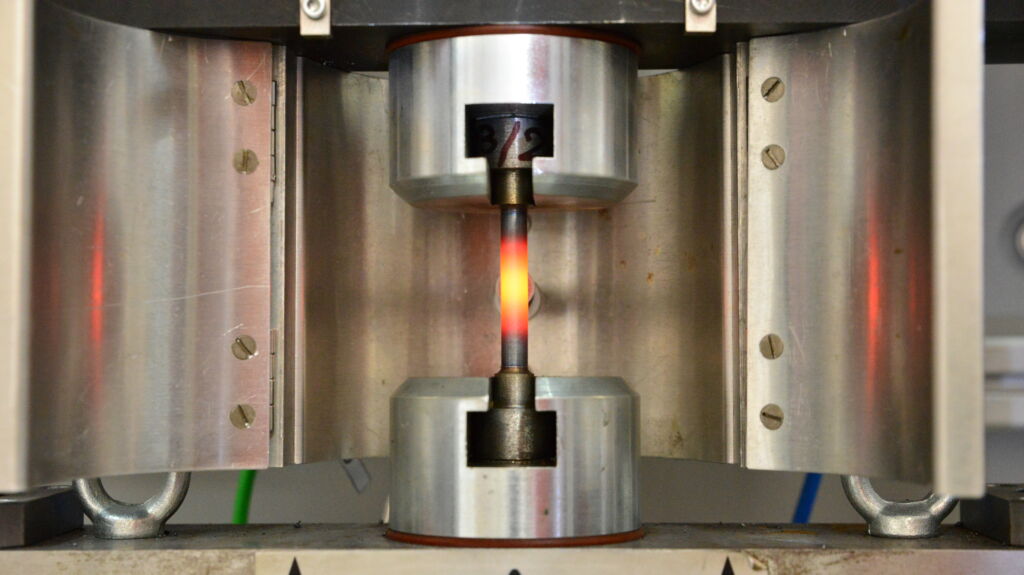
W obszarze prowadzone są badania z zakresu badań podstawowych, rozwojowych i przemysłowych związanych z projektowaniem i wytwarzaniem dedykowanych materiałów konstrukcyjnych i funkcjonalnych z grupy:
- ultra-wysokotemperaturowych kompozytów typu MMC lub CMC w tym kompozytów metalowo-ceramicznych z udziałem materiałów węglowych, węglików, krzemków, borków i azotków;
- nowych lekkich kompozytów na bazie metali wysokotopliwych oraz faz międzymetalicznych i związków międzywęzłowych o ultra-wysokiej odporności na utlenianie, super twardości oraz odporności na zużycie tribologiczne w wysokiej temperaturze;
- materiałów porowatych z nowoczesnych stopów żaroodpornych i żarowytrzymałych do zastosowań w przemyśle lotniczym i kosmicznym (lekkie wymienniki ciepła, materiały uszczelniające, materiały absorbujące energię).
Prowadzone są badania właściwości funkcjonalnych materiałów wysokotemperaturowych przeznaczonych do systemów cieplnego magazynowania energii (TES).
Obszar Badań Korozji Wysokotemperaturowej
W obszarze prowadzone są badania dotyczące degradacji materiałów stosowanych w energetyce oraz w lotnictwie. Prowadzone zagadnienia powiązane są z wykazywaniem mechanizmów degradacji w odniesieniu do dwóch głównych zjawisk: procesów utleniania oraz procesów korozyjnych, które wykonywane są przy udziale atmosfer utleniających (powietrze, para wodna). Inną grupą badań prowadzonych w Instytucie są badania w atmosferach redukujących np. mieszanina Ar oraz Cl2, H2S, SO2 (do 1% obj.), CO2 i inne.
Badane grupy materiałów:
- stopy metali na bazie żelaza, niklu, tytanu, kobaltu i innych stopów żaroodpornych,
- stopy wzmacniane dyspersyjnie wydzieleniami tlenkowymi (stopy typu Oxide Dispersion Strengthened alloys – ODS),
- stopy metaliczne o wysokiej entropii (stopy High Entropy Alloys – HEA),
- stopy metaliczne drukowane za pomocą druku 3D typu Laser Power Bed Fusion (LPBF) i innych.
W laboratorium istnieje możliwość testowania odporności na działanie wysokiej temperatury materiałów metalicznych pokrytych powłokami żaroodpornymi:
- natryskiwanymi cieplnie (np. High Velocity Oxy Fuel (HVOF) Air Plasma Spray (APS),
- nakładanymi z fazy gazowej typu Physical Vapour Deposition (PVD),
- nanoszonymi proszkowo (powłoki dyfuzyjne) z wykorzystaniem aktywnych związków chemicznych typu AlCl3,
- uzyskiwanymi w procesie recyklingu odpadów stalowych z wysoką zwartością Cr.
Obszar Stopów Odlewniczych
W obszarze prowadzone są badania dotyczące zaprojektowania nowoczesnych stopów, które będą charakteryzowały się unikalnymi właściwościami, ściśle dostosowanymi do wymogów użytkowych różnych sektorów przemysłu. Projektowanie, wytwarzanie oraz obróbka cieplna materiałów o zdefiniowanych wielofunkcyjnych właściwościach:
- ze stopów żelaza (staliwo, żeliwo), ze szczególnym uwzględnieniem żeliw umacnianych roztworowo, żeliwa ADI oraz staliw nanostrukturalnych;
- metali nieżelaznych (aluminium, magnez, cynk):
– stopy lekkie, na osnowie aluminium i magnezu, o podwyższonej żarowytrzymałości, stabilności wymiarowej oraz odporności korozyjnej w różnych środowiskach do zastosowań w przemyśle motoryzacyjnym, meblarskim i budowlanym,
– nowej generacji nanomodyfikatory w odlewnictwie stopów metali nieżelaznych jako efektywny sposób podwyższenia właściwości użytkowych materiałów stosowanych w przemyśle transportowym,
– nowe typy stopów na bazie magnezu lub cynku, które cechuje biozgodność oraz kontrolowany czas rozpadu w środowisku płynów fizjologicznych człowieka (biodegradowalność), do zastosowań medycznych;
- nadstopów (niklu, kobaltu) otrzymywanych metodą topienia indukcyjnego w próżni lub obecnością atmosfery ochronnej z zastosowaniem optymalizacji składu chemicznego oraz modyfikacji m.in. Ta, Al, Ti. Opracowanie innowacyjnych technologii (technologia regeneracji przyrostowej, technologia podgrzewania wstępnego), skupiających się na odbudowie strukturalnej nadstopów;
- nowoczesnych stopów wysokoentropowych na bazie aluminium, boru, niklu, kobaltu, miedzi, manganu, molibdenu, żelaza, węgla oraz krzemu np. AlCoCuFeNi, AlCoCuFeNiSi, CoFeMnMoNi, otrzymywanych metodą topienia indukcyjnego z możliwością zastosowania atmosfery ochronnej.
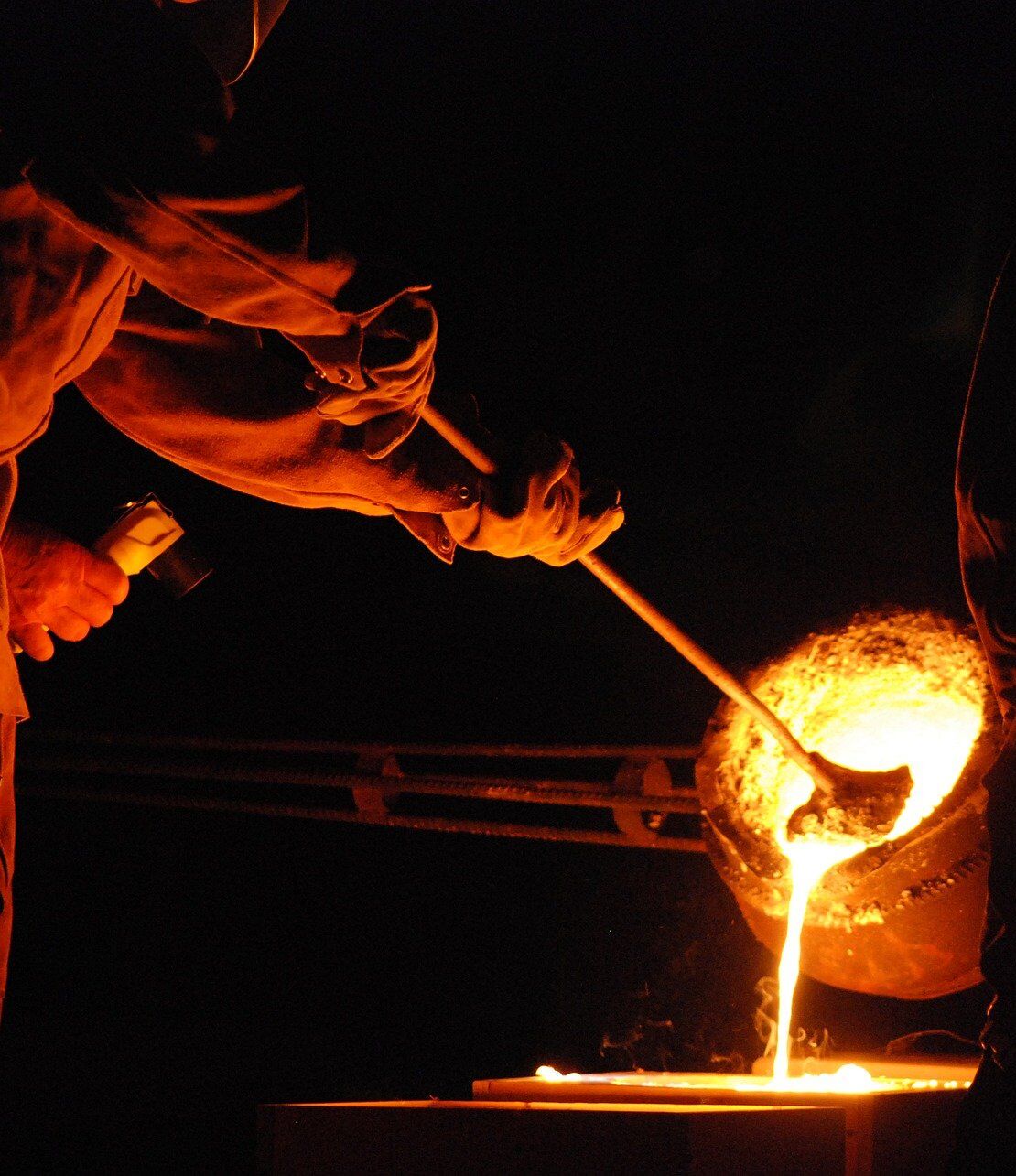
Stopy te dedykowane są dla przemysłu maszynowego, rolnego, górniczego, motoryzacyjnego, lotniczego, zbrojeniowego, energetycznego.
Nowo opracowane materiały będą wykorzystane do wytwarzania komponentów pracujących w środowisku agresywnym, w szerokim zakresie temperatur oraz pod działaniem obciążeń zmęczeniowych. Materiały te mogą również pełnić funkcje zabezpieczające (powłoki funkcjonalne), magazynujące oraz przewodzące. Z uwagi na wielofunkcyjność opracowane materiały będą przyjazne środowisku dzięki niskoemisyjności oraz będą stanowiły tańszą alternatywę dla obecnie stosowanych technologii.
Obszar Projektowania i Prototypowania
W obszarze prowadzone są wirtualne eksperymenty numeryczne dotyczące procesów technologicznych związanych z odlewnictwem, symulacji warunków eksploatacyjnych zjawisk typu Multiphisics oraz zagadnienia optymalizacyjne kształtowania konstrukcji i innowacji procesów odlewniczych. Kształtowanie konstrukcji oraz technologii odlewania z wykorzystaniem systemów modelowania 3D:
- Wykorzystanie systemów MagmaSoft oraz Flow3D do symulacji odlewniczych procesów oraz analiz mechaniki płynów w procesach produkcyjnych. Projektowanie oraz analiza technologii odlewania wysoko i nisko-ciśnieniowego, grawitacyjnego do form trwałych i jednorazowych, odlewania precyzyjnego, w tym z wykorzystaniem modeli wytwarzanych technikami addytywnymi.
- Predykcja powstawania wad odlewniczych wynikających z technologii wytwarzania oraz końcowych właściwości materiałowych i użytkowych odlewu.
- Weryfikacja założeń projektowych z wykorzystaniem numerycznych analiz typu Multiphisics w systemie ANSYS. Optymalizacja topologiczna kształtowania wytrzymałościowego struktury geometrycznej części w oparciu o schemat warunków brzegowych. Sprzężenie analiz termiczno-przepływowo-wytrzymałościowych.
- Modelowanie numeryczne procesów Additive ANSYS Manufacturing z proszków metali. Ocena stanu wytężenia i odkształcenia w trakcie wytwarzania, optymalizacja parametrów pracy oraz wykorzystania materiału z predykcją i ograniczeniem deformacji cieplno-odkształceniowych.
Integracja modelowania numerycznego w cyklu technologicznym zapewnia kompleksowe doradztwo projektowo-techniczne wytwarzania części odlewanych dla przemysłu automotive, lotniczego, wydobywczego oraz energetycznego.
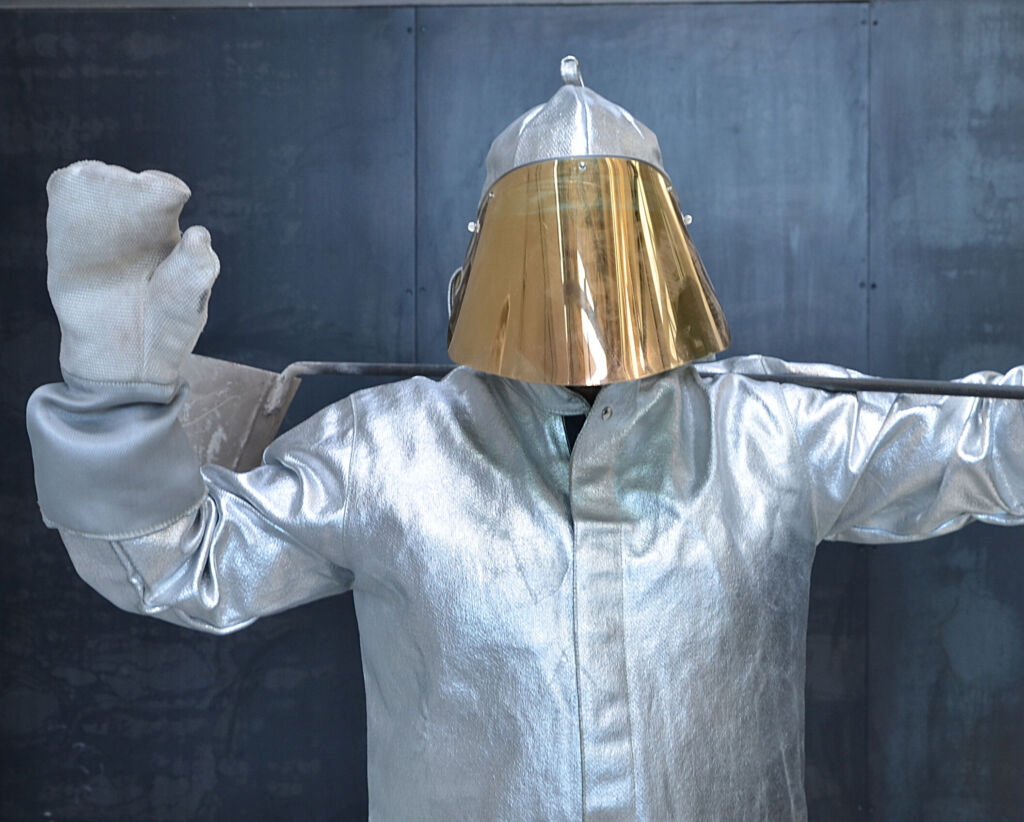
Dodatkowo w obszarze prowadzone są badania dotyczące maksymalizacji możliwości ponownego wykorzystania materiałów odpadowych oraz zmniejszenie szkodliwości procesów odlewniczych. Zagospodarowanie odpadów odlewniczych jest dużym problemem dla odlewni i stanowi znaczne obciążenia finansowe związane z kosztami składowania tych materiałów na wysypiskach. Odpady odlewnicze, a w szczególności zużyta masa formierska, mogą być ponownie wykorzystane w znacznie większym stopniu niż obecnie.
- Definicja i eliminacja najważniejszych strumieni powstawania odpadów w procesach odlewniczych.
- Recykling i zagospodarowanie odlewniczych materiałów odpadowych, w różnych gałęziach przemysłu w celu minimalizacji kosztów produkcji związanych z redukcją zużycia świeżych surowców.
- Proekologia procesów obróbki oczyszczającej odlewów poprzez stworzenie zautomatyzowanego stanowiska do oczyszczania i walidacji powierzchni odlewu z wykorzystaniem technik inżynierii odwrotnej i manipulatorów przemysłowych.
Opracowane technologie wpisują się w politykę zrównoważonego rozwoju oraz gospodarkę obiegu zamkniętego, jak również spełniają zasadę Najlepszych Dostępnych Technik.
Również w obszarze prowadzone są badania zjawisk fizykochemicznych zachodzących w procesach odlewania, opracowywanie technologii z wykorzystaniem nowoczesnych materiałów przeznaczonych na formy i rdzenie odlewnicze.
- Określenie zjawisk zachodzących w procesie formowania warstwy ceramicznej, w aspekcie poprawy jakości powierzchni odlewów i eliminacji wewnętrznych wad odlewniczych.
- Opracowywanie technologii z udziałem nowych generacji ciekłych mas formierskich przeznaczonych na formy do odlewania stopów metali reaktywnych. Modyfikacja spoiw odlewniczych oraz dodatków do mas formierskich.
- Projektowanie innowacyjnych konstrukcji modeli odlewów i komponentów odlewanych, metodami szybkiego prototypowania. Wytwarzanie oprzyrządowania odlewniczego oraz przygotowanie dokumentacji technicznej
i konstrukcyjnej z wykorzystaniem narzędzi inżynierii odwrotnej oraz druku 3D.
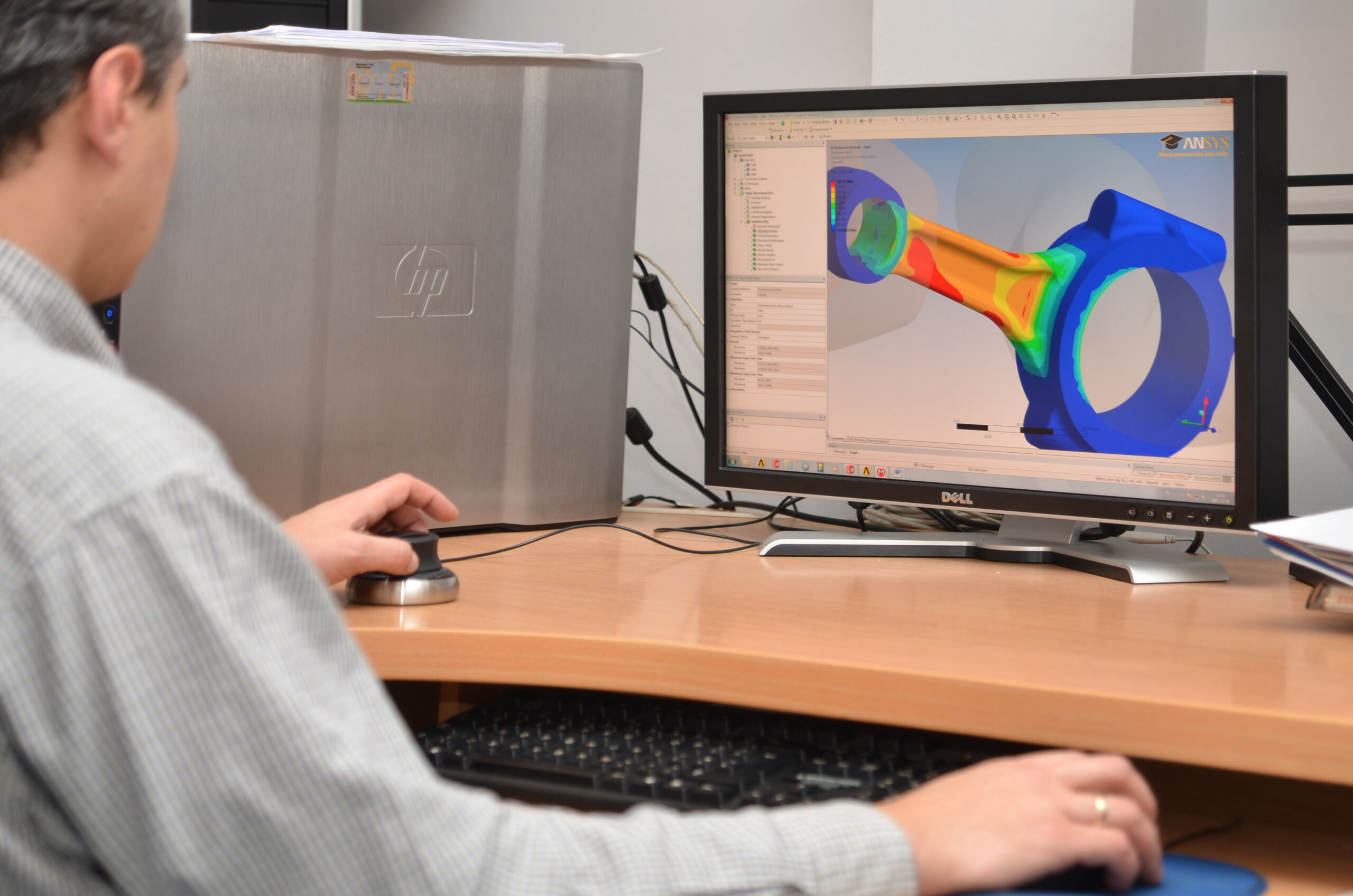
Kontakt
Dyrektor Centrum Materiałów i Technologii Wytwarzania
Dr hab. inż. Daniel Toboła
e-mail: daniel.tobola@kit.lukasiewicz.gov.pl
tel. +48 12 63 17 251