Otrzymywanie materiałów technikami spiekania oraz skanowanie i druk 3D
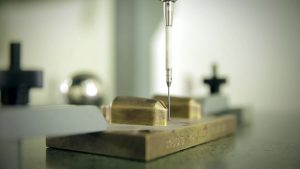
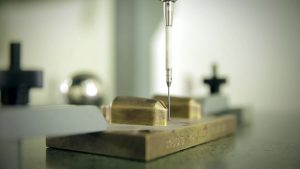
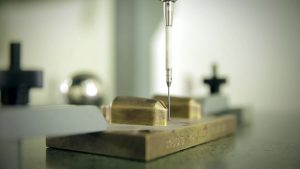
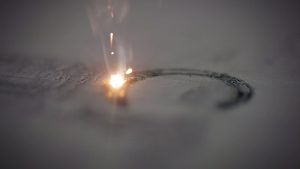
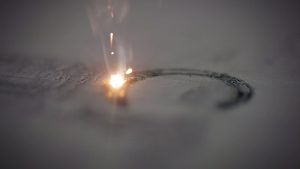
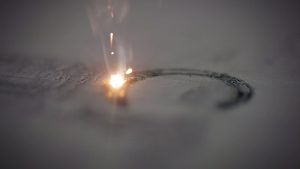
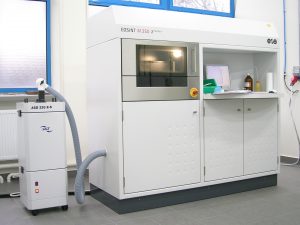
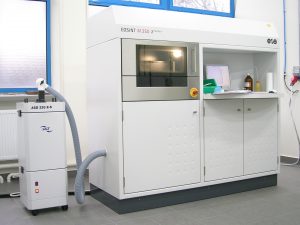
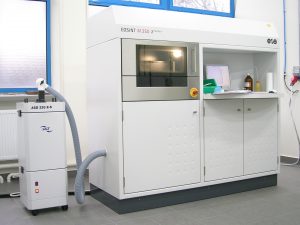
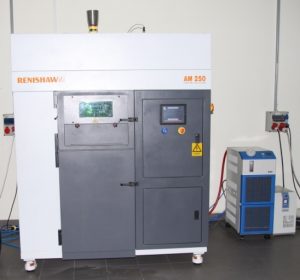
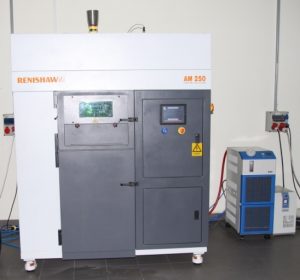
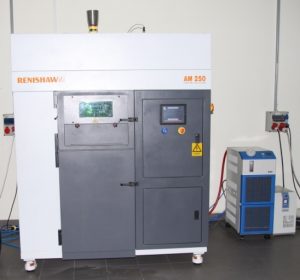
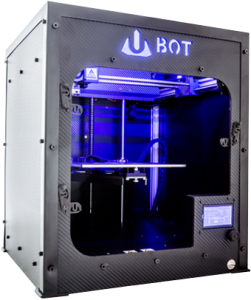
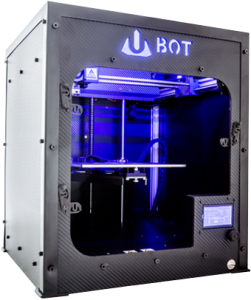
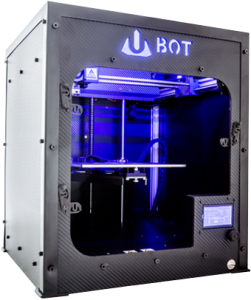
Skanowanie i druk obiektów 3D
Instytut oferuje usługi w zakresie inżynierii odwrotnej (Reverse Engineering), szybkiego prototypowania (Rapid Prototyping) oraz wytwarzania gotowych elementów funkcjonalnych o skomplikowanej geometrii, zarówno z proszków metali i ich stopów metodą selektywnego spiekania i topienia laserowego (Selective Laser Sintering/Melting SLS/SLM), jak i z tworzyw sztucznych i ceramiki w technologii osadzania stopionego materiału (Fused Deposition Modeling FDM) i utwardzania materiałów światłoczułych (Digital Light Processing DLP).
Skanowanie powierzchni i brył obrotowych
Skaner CYCLONE 2 (prod. Renishaw) umożliwia digitalizację danych geometrycznych obiektów fizycznych i uzyskanie komputerowych modeli geometrycznych obiektów rzeczywistych. Uzyskane w ten sposób dane mogą służyć rekonstrukcji bądź modyfikacji wyrobów, które nie posiadają dokumentacji technicznej w postaci rysunków lub modeli przestrzennych 3D. Za ich pomocą można również porównywać wyniki analiz symulacyjnych z danymi rzeczywistymi. Zeskanowane modele wyrobów pozwalają na wykonanie projektów oprzyrządowania technologicznego.
Zastosowanie uniwersalnego połączenia digitalizacji laserowej i stykowej pozwala na uzyskanie danych powierzchni detalu każdego rodzaju. Począwszy od elementów metalowych, drewnianych przez elementy z tworzyw sztucznych do miękkich i delikatnych elementów plastycznych, takich jak: elastomery, guma, tworzywa modelarskie.
Selektywne spiekanie laserowe / selektywne przetapianie laserowe SLS/SLM
Rodzina metod polegających na wytwarzaniu wyrobów w procesie zestalania materiałów w postaci proszku, warstwa po warstwie, który następuje dzięki oddziaływaniu wiązki laserowej na powierzchnię proszku. Są to metody przyrostowe, za pomocą których można wytwarzać elementy funkcjonalne w technologii druku 3D z proszków metali.
Instytut posiada urządzenia pozwalające na produkcję wyrobów najwyższej jakości.
Urządzenie EOSINT M 250 Xt firmy EOS do spiekania laserowego metodą SLS umożliwia:
- przygotowanie pliku STL na podstawie wprowadzonego modelu 3D utworzonego w środowisku CAD
- automatyczny podział modelu na warstwy o określonej grubości
- sprawdzenie i korektę błędów
- dobór parametrów procesu a priori w trybie offline
- wykonanie elementu metodą SLS
Dane techniczne:
- laser CO2: moc ≤ 250 W
- prędkość skanowania: do 3,0 m/s
- grubość nakładanych warstw proszkowych: 20−60 μm
- dokładność otrzymywanych przedmiotów: ±0,05 mm
- maks. wymiary budowanego elementu: 250 × 250 × 200 mm
- gaz osłonowy: azot
Dostępne materiały:
- materiał brązopodobny DirectMetal 20
- stal DirectSteel H20
- stal narzędziowa DirectSteel H20
Urządzenie AM 250 firmy RENISHAW do spiekania laserowego metodą SLS/SLM umożliwia:
- przygotowanie pliku STL na podstawie wprowadzonego modelu 3D stworzonego w środowisku CAD
- automatyczny podział modelu na warstwy o określonej grubości
- sprawdzenie i korektę błędów
- dobór parametrów procesu a priori w trybie offline
- wykonanie elementu metodą SLS
- wykonanie elementu metodą SLM
- opracowanie technologiczne materiałów (parametry „otwarte” urządzenia)
Dane techniczne:
- laser włóknowy: 400 W, długość fali: 10,6 μm
- prędkość skanowania: do 2,0 m/s
- grubość nakładanych warstw proszkowych: 20−100 μm
- dokładność otrzymywanych przedmiotów: ±0,05 mm
- maks. wymiary budowanego elementu: 250 × 250 × 300 mm (X, Y, Z)
- wiązka laserowa o średnicy plamki 70 μm na powierzchni spiekania
Dostępne materiały:
- stal nierdzewna 316L (X2CrNiMo17-12-2 / 1.4404)
- stal Maraging (X3NiCoMoTi18-9-5 / 1.2709)
- stal narzędziowa H13 (EOS: DirectSteel H20)
- stop niklu INCONEL 718
- stop tytanu (Ti grade 5) Ti-6Al-4V
- stop aluminium AlSi10Mg
- czysty tytan (Ti grade 2) CP-Ti gr2
- materiał brązopodobny EOS-Direct Metal 20
Instytut oferuje usługi z zakresu druku w 3D w technologii FDM (Fused Deposition Modeling) oraz w technologii DLP (Digital Light Processing).Technologia FDM (Fused Deposition Modeling) wykorzystuje w procesie wytwórczym termoplasty, czyli tworzywa sztuczne wykorzystywane do formowania geometrii w wysokich temperaturach. Modele drukowane w tej technologii powstają przez nakładanie kolejnych warstw półpłynnego materiału, który jest wytłaczany (ekstrudowany) z podgrzewanej dyszy. Materiał ma formę żyłki o stałej średnicy (1,75 mm lub 2,85 mm) nawiniętej na szpulę (filament). Technologia DLP (Digital Light Processing) to druk 3D polegający na utwardzaniu materiałów światłoczułych/żywic (fotopolimerów) za pomocą światła projektora.Drukarka FDM (Fused Deposition Modeling) − model UBOT 3D
Dane techniczne:
- obszar roboczy: 250 mm × 250 mm × 250 mm
- dokładność pozycjonowania osi X, Y: 6,25 μm, Z: 0,6 μm
- średnica dyszy: od 0,2 mm do 1,2 mm (wymienne dysze)
Dostępne materiały:
- PLA oraz inne o niskim skurczu
- Drukarka DLP (Digital Light Processing) − model Anycubic Photon S
Dane techniczne:
- obszar roboczy oś X: 115 mm, Y: 65 mm, Z: 165 mm
- dokładność wydruku warstw: 25 μm (0,025 mm)
Dostępne materiały:
- żywice polimerowe utwardzane wiązką światłą o długości 405 nm
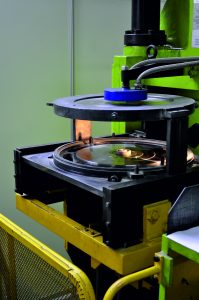
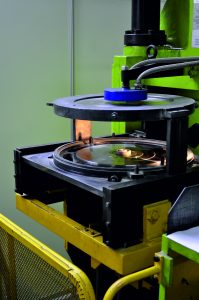
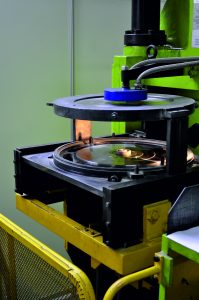
Spiekanie HPHT High Pressure High Temperature
Spiekanie wysokociśnieniowe HP-HT stosuje się do materiałów supertwardych, takich jak diament i regularny azotek boru (cBN), przeznaczonych na ostrza narzędzi, ale także do innych materiałów np. nanoproszków i materiałów wysokotopliwych.W Instytucie znajduje się hybrydowe urządzenie HPHT-SPS wyposażone w komorę typu Bridgmana umożliwiające zastosowanie zarówno nagrzewania konwencjonalnego prądem przemiennym 50 Hz, jak i prądem impulsowym wysokiej częstotliwości. W zależności od objętości spiekanego materiału możliwe jest spiekanie proszków pod ciśnieniem do 4 GPa lub w zakresie 4−8 GPa oraz w temperaturze do 2400°C. Urządzenie umożliwia płynne podnoszenie temperatury z równoczesnym wzrostem ciśnienia, i odwrotnie, możliwe jest jednoczesne płynne obniżanie ciśnienia i temperatury. Jest to unikatowe rozwiązanie dla tego typu aparatury, ograniczające powstawanie naprężeń cieplnych w materiałach spiekanych.Objętość spiekanego materiału wynosi 1 lub 16 cm3. Materiał umieszczany jest w grzejniku grafitowym o średnicy wewnętrznej 15 lub 27 mm (niekiedy stosowane są specjalne folie izolujące od wpływu grafitu), a następnie w specjalnym wsadzie reakcyjnym, zapewniającym kontakt elektryczny i pseudoizostatyczne warunki spiekania.Przedmiotem zamówienia może być opracowany produkt w postaci materiału bądź usługa opracowania technologii wytwarzania różnych materiałów
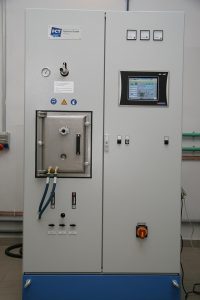
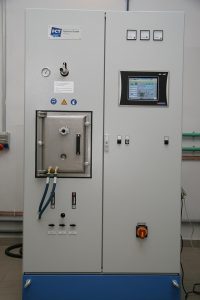
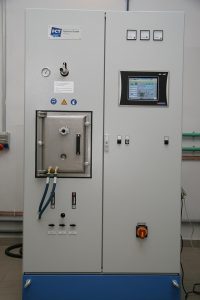
Spiekanie SPS Spark Plasma Sintering
Jedna z najnowocześniejszych metod spiekania proszków umożliwiająca kształtowanie materiałów bez potrzeby przeprowadzenia wstępnego prasowania i izostatycznego dogęszczania. Cechą charakterystyczną jest wykorzystanie bezpośredniego nagrzewania proszków przepływającym prądem.Aparatura SPS HP 5 firmy FCT umożliwia spiekanie szerokiej grupy materiałów ceramicznych i metalicznych oraz kompozytów na ich bazie oraz prowadzenie procesów w zakresie niższych temperatur i niższego ciśnienia w porównaniu do spiekania swobodnego lub procesu prasowania na gorąco:siła nacisku maksymalnie od 2 do 50 kNmożliwość regulacji szybkości przesuwu tłoka w zakresie od 0 do 2 mm/smożliwość zastosowania różnych zestawów narzędzi do spiekania próbek o średnicy 10, 20 i 30 mmmaksymalna temperatura spiekania 2400°C (dla matrycy o średnicy 10 mm maksymalna temperatura wynosi 1100°C)szybkość grzania w zakresie od 5 do 400°C/minpomiar temperatury procesu przy użyciu pirometru, miejsce zamocowania pirometru w osi próbki, pomiar w bezpośrednim sąsiedztwie próbkialternatywna kontrola i pomiar temperatury przy użyciu termoelementu typu Kmożliwość prowadzenia procesu spiekania w warunkach próżni o wartości 5 × 10-1 mbarmożliwość prowadzenia procesu spiekania w atmosferze ochronnej azotu lub argonu, przy ciśnieniu w zakresie od 0 do 1100 mbarmożliwość regulacji czasu trwania impulsuautomatyczne sterowanie oraz kontrola siły prasowania, przemieszczenia stempla, temperatury oraz parametrów impulsów
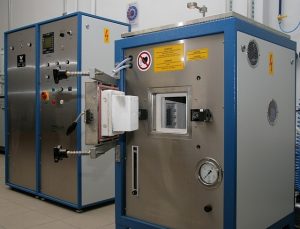
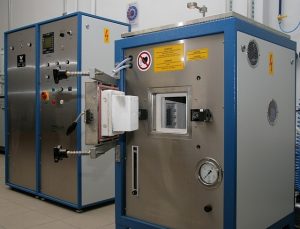
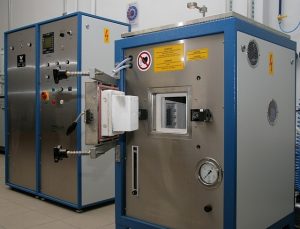
Spiekanie mikrofalowe
Spiekanie mikrofalowe jest metodą spiekania proszków wykorzystującą energię mikrofal do jednorodnego nagrzania spiekanego materiału.Piec mikrofalowy MKH-4,8 firmy LINN, przeznaczony jest do spiekania szerokiej gamy materiałów metalicznych, ceramicznych i kompozytowych w atmosferze azotu, argonu lub próżni w zakresie temperatur do 1850°C.Parametry techniczne:moc 4,8 kW; 6 magnetronów zapewnia jednorodny rozkład fal w komorzepłynna regulacja mocy magnetronów w zakresie od 15% do 100%częstotliwość 2,45 GHzkomora umożliwiająca pracę w atmosferze ochronnej o maks. nadciśnieniu 5 mbar oraz w warunkach próżni o wartości maks. 10-4 mbarwymiary komory: 135 × 135 × 135 mmwymiary otworu wsadowego: 135 × 135 mminstalacja podawania gazów obojętnych: azot, argonszybka inspekcyjna o średnicy 20 mm w drzwiach, do kontroli wizualnej aktualnie realizowanego procesuizolacja termiczna funkcjonująca do maksymalnej temperatury 1850°Cpirometr do kontroli temperatury w zakresie od 35°C do 2500°Ctermoelement do kontroli temperaturyprogramator do sterowania procesem zawierający 25 programów oraz 50 segmentów na każdy program
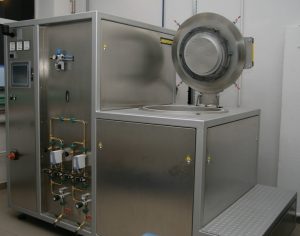
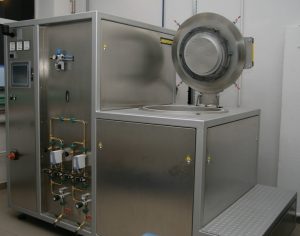
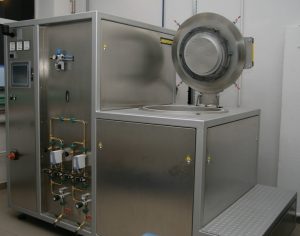
Spiekanie konwencjonalne (swobodne)
Instytut posiada kilka urządzeń pozwalających na spiekanie swobodne materiałów z zastosowaniem próżni, atmosfery utleniającej, azotu lub argonu, w temperaturze do 2200°C:
- Piec VHT08-20 W TL firmy Nabertherm
- Piec próżniowy MOV firmy Balzers
- Piec z atmosferami ochronnymi HTK8 firmy Gero
- Piec Nabertherm HT16/18